How Hydropower Maintenance Enhances Reliability
November 2, 2024
Explore hydropower maintenance essentials, from inspections to efficiency tips for optimal performance.
.jpg)
Understanding Hydropower Maintenance
Effective hydropower maintenance is crucial for the longevity and reliability of hydroelectric facilities. Proper upkeep ensures optimal performance and minimizes the risk of breakdowns.
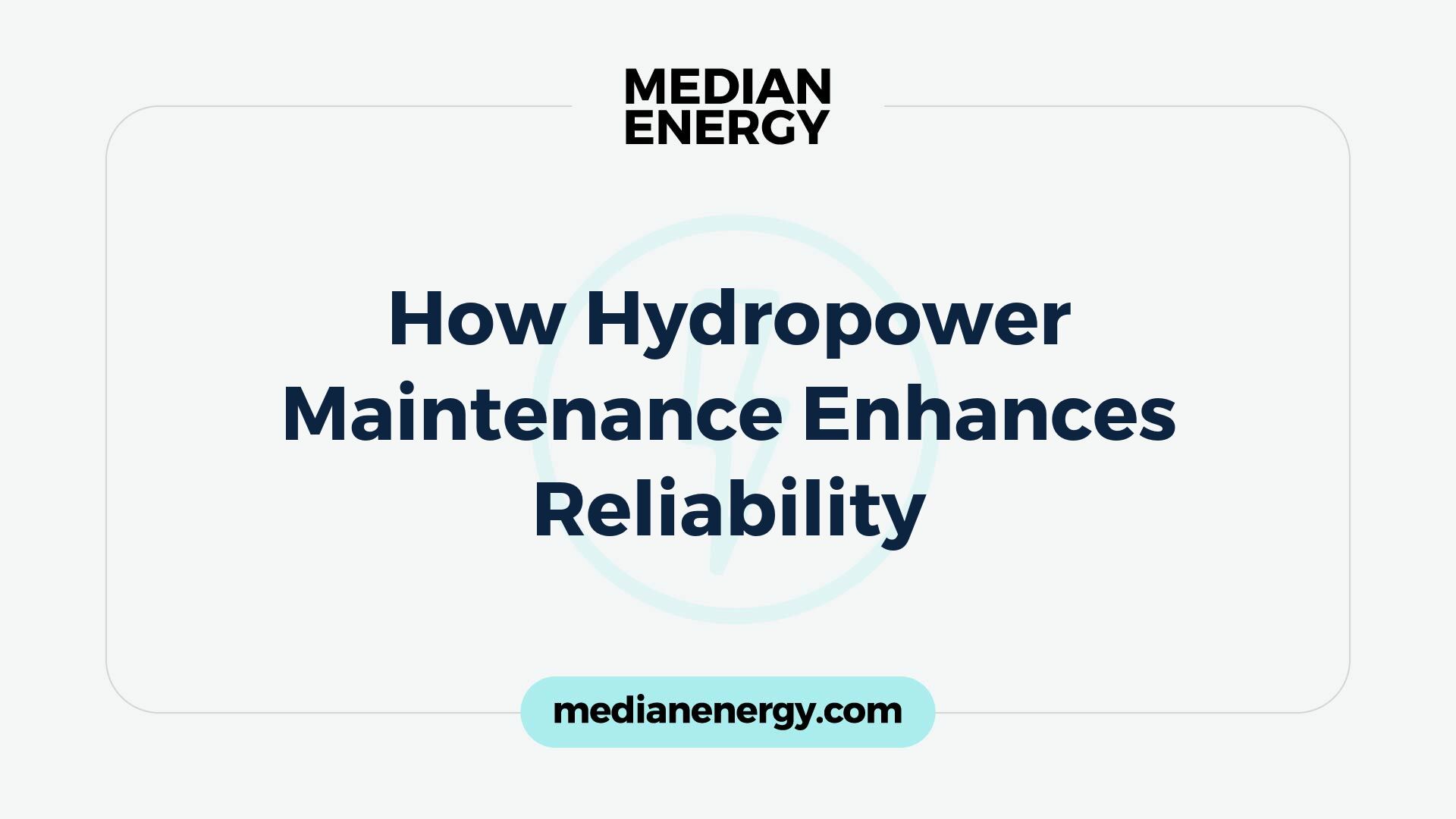
Importance of Regular Maintenance
Regular maintenance plays an essential role in the operational success of hydropower systems. It helps in identifying potential issues before they escalate into significant problems. Consistent checks also improve safety standards and operational efficiency, leading to enhanced energy production.
Factors Influencing Maintenance Needs
Several factors can impact the maintenance requirements of hydropower systems. Understanding these elements allows for tailored maintenance strategies to meet specific needs.
By being aware of the importance of regular maintenance and the factors that influence its needs, hydropower operators can implement effective maintenance strategies that ensure both safety and efficiency.
Inspection and Monitoring
Inspection and monitoring are crucial components of hydropower maintenance. Regularly assessing the condition of equipment and systems ensures optimal performance and minimizes downtime.
Routine Inspections
Routine inspections involve regular checks of all equipment and infrastructure associated with the hydropower facility. This includes visual assessments, operational checks, and functionality tests. The frequency of inspections can vary based on the type of equipment and regulatory requirements.
Regular inspections help to identify potential issues early, thereby allowing for timely interventions and reducing the risk of significant failures.
Monitoring Equipment Performance
Monitoring the performance of hydropower equipment is essential for maintaining efficiency and reliability. This can be accomplished through various methods, including the use of sensors and performance data analysis.
Key performance indicators (KPIs) are often monitored to assess the functionality of equipment. Some common KPIs for hydropower systems include:
By consistently monitoring these indicators, potential problems can be detected before they escalate. Data gathered during monitoring can guide maintenance strategies, ensuring that the hydropower facility operates at optimal capacity.
Preventive Maintenance
Importance of Preventive Maintenance
Preventive maintenance plays a crucial role in the overall management of hydropower systems. By implementing regular maintenance practices, operators can identify potential issues before they escalate into significant problems. This proactive approach helps to extend the lifespan of equipment, reduce the risk of unexpected failures, and ultimately enhance the reliability of the hydropower plant.
The benefits of preventive maintenance include:
- Cost Savings: Addressing issues early can prevent costly repairs and downtime.
- Increased Efficiency: Well-maintained equipment operates more efficiently, maximizing energy production.
- Safety Enhancement: Regular checks ensure that all machinery operates safely, reducing the risk of accidents.
Scheduled Maintenance Tasks
Implementing a schedule for maintenance tasks ensures that all components of a hydropower system receive the attention they require. Below is a table that outlines common scheduled maintenance tasks, their frequency, and the purpose of each task.
Each task is designed to monitor and maintain specific components of the hydropower system, guaranteeing optimal operation. By adhering to a structured maintenance plan, operators can effectively manage hydropower maintenance, enhancing performance and ensuring long-term sustainability.
Reactive Maintenance
Reactive maintenance refers to the actions taken to address unexpected issues that arise during the operation of hydropower facilities. This approach is critical for ensuring the continued functionality and safety of the equipment involved.
Addressing Unexpected Issues
When unexpected problems occur, prompt and effective interventions are necessary. Common issues in hydropower systems can include equipment malfunctions, leaks, or structural failures. Identifying the root cause quickly is essential for minimizing downtime and restoring operations.
A team of skilled technicians is typically deployed to conduct assessments and execute repairs. Effective communication among team members and stakeholders ensures that all parties are informed of the situation and the steps being taken.
Response Time and Protocols
Quick response time is crucial in reactive maintenance to mitigate potential risks and costs. Establishing clear protocols can facilitate efficient handling of issues as they arise. A response protocol may include the following steps:
Timely and structured responses not only reduce downtime but also enhance the overall reliability of hydropower operations. By implementing robust protocols, facilities can improve their reactive maintenance capabilities, ensuring efficient resolution of unforeseen challenges.
Safety Measures
Safety is a critical component of hydropower maintenance. Implementing thorough safety procedures and establishing proper training requirements can help reduce the risk of accidents and ensure a safe working environment for all personnel involved.
Safety Procedures During Maintenance
Clear and effective safety procedures must be established and followed during maintenance activities. These procedures typically include the following elements:
Training Requirements
Training is essential for maintaining a safe working environment during hydropower maintenance. All personnel should receive comprehensive training in the following areas:
Implementing robust safety measures and ensuring all personnel receive the necessary training are vital to promoting a culture of safety within the hydropower maintenance industry. Ensuring this level of preparedness can significantly reduce risks and enhance the safety of all maintenance activities.
Increasing Efficiency Through Maintenance
Efficiency in hydropower facilities can be significantly enhanced through effective maintenance strategies. This section will cover optimal practices for maintaining equipment and the importance of upgrading and modernizing systems.
Optimal Practices for Efficiency
Implementing optimal practices for maintenance ensures that hydropower operations run smoothly and efficiently. Regular evaluations of equipment and systems contribute to higher energy output and reduced operational costs.
Upgrading and Modernizing Equipment
Modernizing equipment is vital for maintaining efficiency in hydropower systems. Old technology may hinder performance and contribute to increased maintenance costs.
By applying these practices and considering upgrades, hydropower facilities can operate more efficiently while ensuring reliable energy production.
Sources
https://www.gevernova.com/secure-extend
https://www.hallidayshydropower.com/hydropower-maintenance
https://www.protemusa.com/industries/hydropower